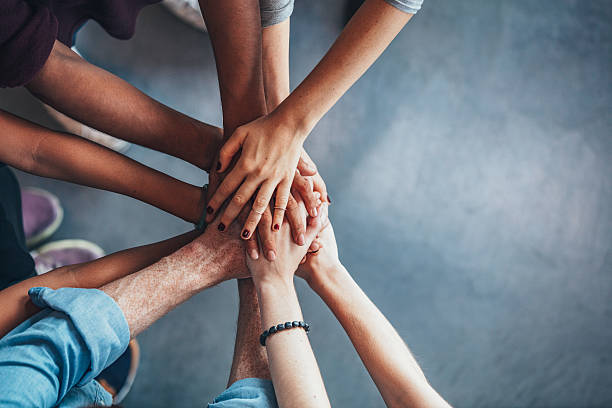
This course focuses on creating and nurturing a collaborative and inclusive team environment within the context of process improvement initiatives and how teamwork culture can help you get there. A successful teamwork culture can be described as an environment marked by the shared belief that the organization can move forward most effectively when collaboration, cooperation, and engagement are at the heart of thinking, planning and decision making.The test can be conveniently taken from the comfort of one’s home, library, or workplace. Upon successful completion and passing of the test a digital certificate will be issued to validate one’s achievement.
Course Overview
1.Background
2.What is Teamwork Culture?
3.Attributes of Teamwork Culture Successes in Organizations
4.What Leaders and Managers can do
5.8 Strategies to Build strong Teamwork Culture
6.How to Improve Teamwork Between Quality & Manufacturing Organizations
7.Why is Teamwork Culture Important in the Workplace?
8.Building a Culture of Teamwork
9.Growing a Culture of Teamwork
10.Making Your Culture of Teamwork a Success
11.Benefits of Teamwork Culture
12.Disadvantages of Teamwork Culture
13.Application & Conclusion
14.Sources
Course Objective
Upon completion of this course you will be able to:
- Understand the importance of teamwork culture in the context of Six Sigma and Lean Manufacturing methodologies
- Learn techniques for building and leading high-performing teams in a Six Sigma and Lean Manufacturing environment
- Gain knowledge of the key elements of a successful teamwork culture and its impact on process improvement
- Develop skills in fostering effective communication, collaboration, and cooperation among team members
- Apply teamwork principles and techniques to real-world case studies and practical exercises to reinforce learning and develop proficiency
- Understand the connection between teamwork culture and employee engagement, satisfaction, and retention
Target Audience:
Teamwork Culture can be used can be used by anybody who is involved in process improvement such as business analysts, engineers, project managers, advisors, maintenance, facilities and operation.
Estimated time to complete:
Open format, self-paced